There are approximately 340,000 wind turbine generators (WTG) throughout the world: 320,000 onshore and 20,000 offshore. The power output of the majority of these are 1.5 MW to 2.5 MW. The evolution of wind power has largely been about designing and building bigger blades and placing them atop higher and higher towers to engage stronger and more consistent winds to improve energy capture. Unfortunately, in most countries, including the U.S., laws limit the overall height of a WTG on land to 100 meters (328 feet).
The current solution is offshore wind. Other than height restricted areas surrounding airports, offshore wind farms have no height restrictions. In the foreseeable future, wind-turbine developers will be installing huge 10-12 MW turbines in their offshore wind farms. The benefits of large offshore WTGs can only be realized if stronger and lighter materials with longer lifespans are developed.
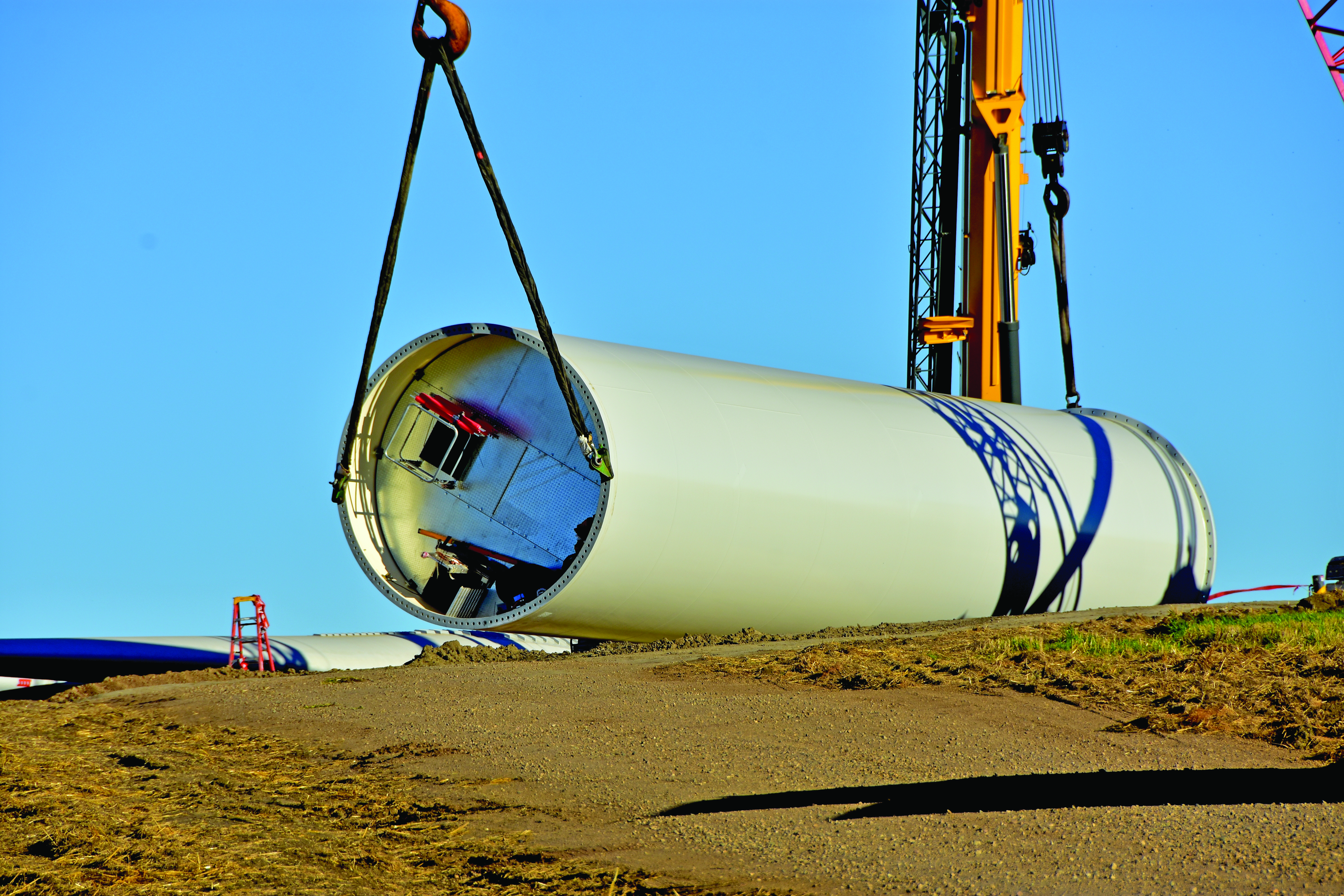
A New Concrete Tower Concept
Of all the WTG towers in the world today, less than 2 percent are constructed in concrete. Although concrete is an extremely well understood material with a thoroughly developed industry behind it, traditional concrete towers are heavier and costlier than those built of steel due to the design requirements to include heavy-coated steel rebar with thicker concrete cover. The new generation of towers required for larger offshore turbines needs to be produced with stronger, lighter materials while still withstanding the harsh conditions of the marine environment. Geopolymer concrete and basalt rebar are those materials.
Ordinary Portland cement (OPC) is the binder (paste) that holds a traditional Portland concrete mix together. Geopolymer cement binders are used commercially elsewhere in the world due to their superior performance to OPC binders. Geopolymer cement is a perfect choice for its ability to bond with basalt rebar both mechanically and chemically to develop the strength characteristics required for this new generation of turbine tower. Basalt rebar is three times stronger and four times lighter than steel rebar. For a similar diameter in steel rebar, basalt rebar is seven to nine times lighter for an equal strength replacement.
In existing marine concrete structures, the greatest threat is water, either fresh or salt. Over time, water penetrates concrete due to its natural porosity through unseen cracks and eventually rusts the rebar skeleton. Even protected rebar has coating failures, and deterioration eventually causes the steel to fail. Seawater directly attacks the chemistry of OPC causing rapid failure. The large amounts of calcium compounds comprising OPC (approximately 79 percent) comes under attack by the sulphur compounds in seawater, essentially rotting the concrete. The OPC binder in a traditional concrete mix can occupy up to 20 percent of the mass of the concrete. Replacing the OPC in the concrete mix design with a geopolymer binder will foil the degradation scenario by minimizing the calcium compound in its chemical composition.

New Materials of Concrete Mix Design
The geopolymer cement binder is made up of four inexpensive and widely available components: type-2 fly ash, fresh water, waterglass (sodium-silicate), and lye (sodium hydroxide). Using type-2 slag fly ash, the geopolymer cement binder can have as little as 2 percent calcium, producing a saltwater-resistant material. In general, these cements are stronger and both fireproof and waterproof. They bond well to most materials, have minimal expansion or contraction, are formable (with the correct superplasticizers), and are resistant to salt, acids, and alkalis.
The production process for producing geopolymer has an approximately 80 percent smaller carbon footprint than OPC. This is significant since, according to Clatham House, a top think-tank in London, the production of OPC binder currently accounts for approximately 8 percent of the world’s carbon dioxide emissions. Wind is considered a clean energy source but not if the production of the wind generators is contributing to the emissions associated with climate change.
To replace the steel rebar, a nonmetallic bar made from readily available basalt (stone) is used for reinforcement. Basalt stone (generic solidified volcanic rock) is found all over the Earth and is a key component of the mix, enabling the 100-year minimum durability of the turbine tower structure. The basalt stone, when heated to a temperature of 1,800 degrees, turns to a liquid that is run through a palladium die that produces soft flexible threads. The threads are laid in parallel and locked together with an epoxy, producing basalt rebar — a waterproof, chemical-resistant, fireproof material with a tensile strength several times stronger than steel. The geopolymer binder in the concrete binds to the basalt rebar on a chemical level in addition to the mechanical bonding. The basalt rebar is extremely light and also fairly flexible, lending to easy placement in the structure. Basalt fiber, much like nylon fiber, is chopped into variable lengths (6-25mm) and used in the mix design for added strength.

Concrete Mix Design
The key to the constructability of the tower components is the concrete mix design. The mix has to be efficient to wet-out and bind to the basalt rebar and the chopped basalt fiber for low temperature crack resistance. Geopolymer cement (the paste) has a high viscosity. To achieve its workability, its placement will need a super-plasticizer. A new hybrid super-plasticizer has been designed for geopolymer cement using rice husk and an alkaline that makes it possible to achieve the correct viscosity for placing the mix into the slipform.
The geopolymer cement (binder) will make up 20 percent of the concrete mix. Replacing standard silica sand will be measured granite sawdust. This will have beneficial effects on the composite strength, as well as the modulus of elasticity. The specific gravity of the silica sand is 2.83, whereas the granite ranges from 2.65 to 2.85, so the final mix is lighter. The porosity of silica sand is 25 to 30 percent and holds unwanted water in the mix design, whereas the porosity of granite is almost zero (0.25 percent). The final aggregates will be crushed granite (3/16 to 1/4 inch). This mix can be fined-tuned to achieve high strength and density in the tower components. The wind tower will have a minimum of a 100-year life due to the low porosity, high strength, and cure technology found in the binder in this new concrete mix design.
Tower Construction
Construction of the WTG tower is mobilized near the harbor where the WTG will be deployed, solving the insurmountable challenge of transporting tower segments made of steel. Steel-tower segments for these larger WTGs will be too heavy with too large a circumference for highway and rail transportation. Taller towers require thicker steel rolled plates with increased weight and larger base circumferences. The average weight of one segment of a three-segment steel turbine tower is approximately 400 tons, with a length of 130 feet and a diameter of 29.5 feet at the bottom and 16.5 feet at the top. Transportation of the tower to the wind farm becomes a major consideration with 4.5-meter (14 feet, 10 inches) maximum clearance for bridges in the U.S., not to mention the higher axel requirements on local and interstate roads.

Producing this new concrete tower is achieved using a slipform construction system that consists of a precast starter bottom and a top makeup attachment ring. Both components will have exposed rebar cages with the correct lap requirement. This construction system will use local labor to transport and place all the materials required using a rack-and-pinion man and material hoist. Mobile batch plants can easily be set up within the back lots of the harbor to deliver high quality concrete or, if preferred, a volumetric truck mixer can be used. When the tower sections being slip formed are complete, they will be released from their holding slab and placed horizontally on a multi-axel transport dolly and transported to an assembly area for placement and installation of internals. Once this operation is complete, the tower sections are within the harbor, to the quay, and placed on an ocean- going deck barge for final assembly at the deep water deployment site.
Its tubular tapering form will provide excellent vertical load capacity. The wind loads affecting the overturning and bending of the tower will be resisted by the compression of the externally imposed forces, as well as the high-strength basalt rebar reinforcement. The mechanical and chemical bonding of the geopolymer cement to the basalt rebar allows for the transfer of forces from the reinforcement skeleton into the body of the concrete mix design. This allows the basalt rebar to work not only in tension, but it can increase compression value as much as 10 to 15 percent. There are no durability issues to overcome using basalt rebar. The new materials selected allow the tower-wall thickness to be determined by concrete cover to rebar rather than the necessary strength to stiffness required by traditional structural design requirements. The method of design and construction will allow for the attachment of the stanchion’s connection for the tower zone internals as well as increase the section modules of the wall through structural considerations in the design of the rebar skeleton.
Conclusion
To meet the energy needs of a growing global society, wind-turbine developers will be installing huge 10 to 12 MW turbines. Our new generation of wind turbine towers and floating foundations will address this need. Using geopolymer concrete and basalt rebar creates a substantially lighter yet stronger concrete than current OPC structures. The turbine tower zone components are designed to withstand the sea state and wind loads for more than a 100-year minimum to support a minimum of three generations of WTG change outs. This new concrete tower concept will target the offshore market but can easily be adapted to onshore projects when higher height permits materialize.
About the author
Andy Filak is a principal with AMF Concepts. He has spent the last nine years developing concepts for fixed and floating systems for offshore wind. Prior to that, he owned Formwork Engineering with offices in Seattle, Washington; London, England; and Los Angeles, California, as a formwork contracting company. He can be reached at Amfconcepts@gmail.com or 310-373-5004.